Comparative failure characterisation
Comparative failure characterisation is an essential tool in the preliminary diagnosis of problems in industrial materials and components.
At INFINITIA Industrial Consulting, we use this methodology to compare failed samples (NOK) with non-failed samples (OK), with the aim of identifying key differences in their physical, chemical or mechanical properties that may be related to the origin of the failure.
Our comparative failure analysis laboratory has a team specialised in the use of advanced techniques and a methodological approach based on forensic engineering, which allows us to offer reliable and useful results for industrial decision-making.
What does comparative failure characterisation consist of?
At INFINITIA, we approach comparative failure characterisation through a sequence of analyses that begins with a visual inspection of the materials to identify apparent defects, such as lack of homogeneity, inclusions or surface alterations.
Subsequently, chemical, physical and mechanical characterisation techniques are applied, such as spectroscopy, electron microscopy or hardness and impact tests, to detect possible differences between samples.
This approach does not aim to determine the definitive failure mechanism, but rather to identify critical disparities between materials, which is a key step in focusing subsequent more specific studies.
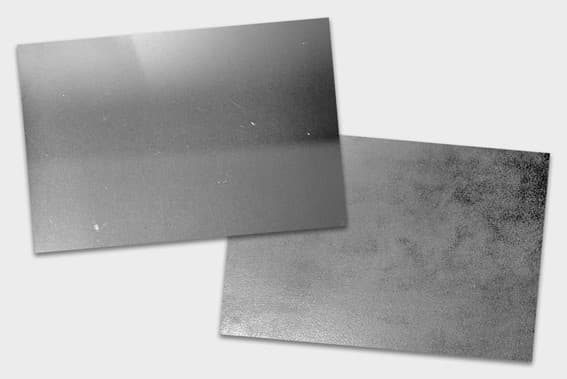
Advantages of comparative failure characterisation
One of the main benefits of this service offered by INFINITIA is the ability to anticipate structural failures in industrial components, improving the reliability of the final product.
For example, in sectors such as automotive or electronics, detecting a variation in the chemical composition or heat treatment of a defective batch can prevent product recalls or significant economic losses. In addition, this technique allows us to evaluate the quality of new suppliers, validate production processes or document failures in the event of complaints.
INFINITIA adds value to the process by combining technical knowledge, sector experience and comparative analysis.
Comparative failure characterisation at INFINITIA
At INFINITIA, we have an industrial laboratory equipped with state-of-the-art technology to carry out comparative characterisations of materials with the utmost precision.
Our approach is based on a rigorous methodology: from initial visual assessment to detailed comparison of critical properties between NOK and OK samples. We adapt to each case to provide a solid preliminary diagnosis, aimed at identifying potential causes of failure and defining the next steps for investigation.
This capability makes us a strategic partner for companies seeking technical and agile solutions to quality or reliability issues with their products.
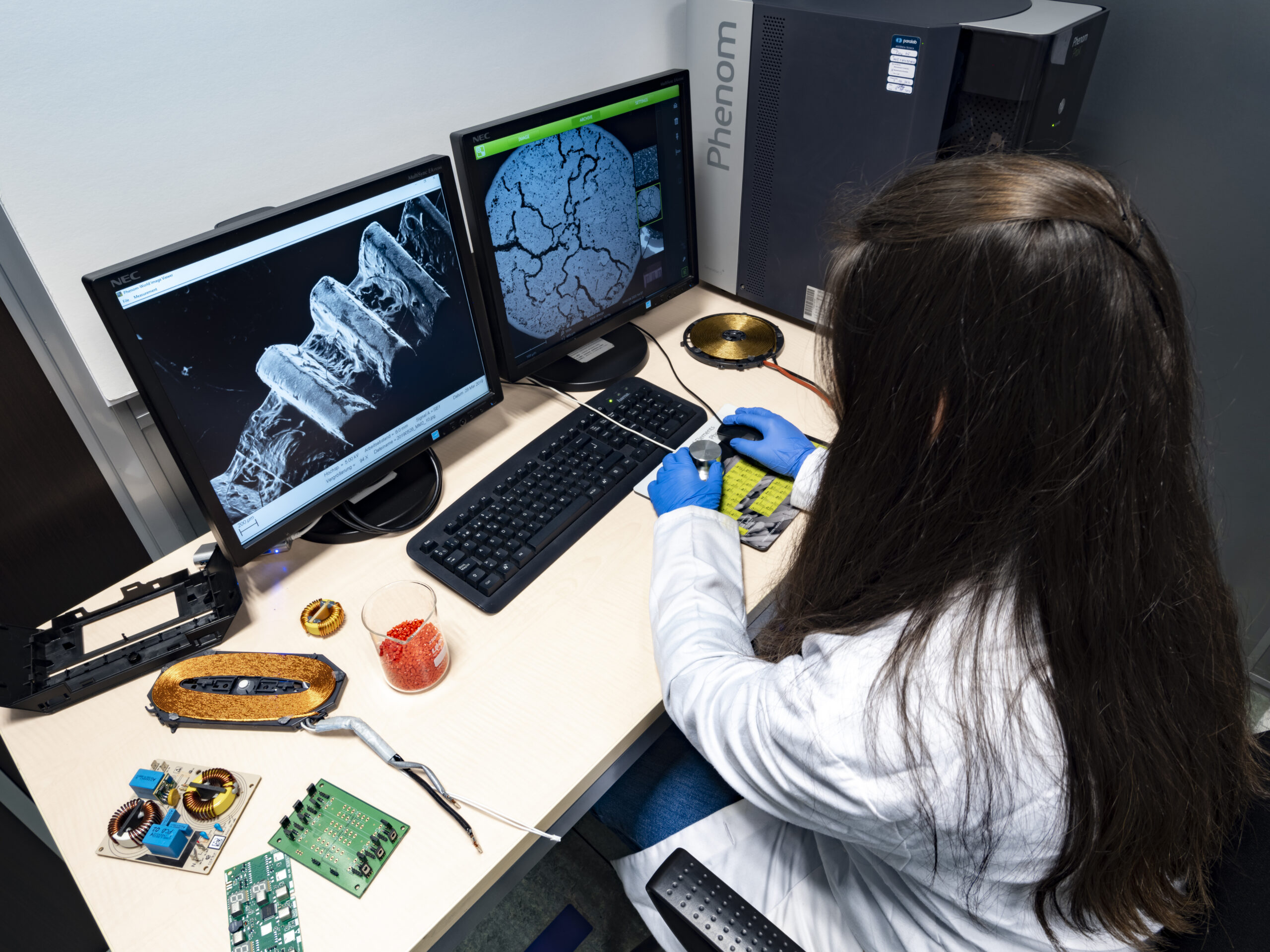
Types of comparative failure characterisation tests
At INFINITIA, we carry out various comparative failure characterisation tests to identify significant differences between defective (NOK) and reference (OK) samples. These studies allow us to detect variations that may be related to the observed failure, even if the final mechanism is not determined.
Our goal is to provide our customers with objective and accurate information to make informed decisions in their industrial processes.
Comparative chemical composition and structure tests
Using techniques such as FTIR, XRF, AAS or SEM-EDS, we compare the chemical composition of the failed sample and the reference sample. This type of analysis is useful for detecting contamination, formulation changes or differences in additives.
For example, in a study of failures in plastic coatings, FTIR spectroscopy detected the presence of unauthorised plasticisers in the defective parts, which were responsible for the loss of adhesion of the coating.
Morphological analysis and microscopy tests
We use optical microscopy, SEM and image analysis to compare the microstructure and morphology of surfaces between OK and NOK samples. We detect defects such as microcracks, porosity, inclusions or lack of homogeneity.
A typical case was the analysis of premature cracks in hardened steel parts. Microstructural comparison revealed an irregular phase distribution due to poorly controlled heat treatment in the defective parts.
Comparative mechanical tests
We perform tensile, impact, hardness and bending tests to assess whether there are mechanical differences that explain the occurrence of the failure. We compare limit values and behaviour under load.
At INFINITIA, we use these tests to verify differences in strength between batches of plastic housings, detecting that a batch with lower hardness values caused breakage under impact in everyday use.
Thermal and stability tests
Tests such as DSC, TGA or TMA allow us to compare the thermal behaviour of materials when exposed to heat, revealing differences in stability, phase transitions or degradation.
For example, in a case of thermal deformation failure in electronic components, DSC detected that the material of the defective sample had a glass transition temperature lower than specified.
Corrosion and accelerated ageing tests
We simulate extreme conditions to compare the performance of coatings or materials in contact with aggressive environments (salt spray, humidity, thermal cycles). This allows us to identify defective surface treatments.
In a study for the electric mobility sector, metal coatings on connectors exposed to salt spray showed premature failure. Comparative analysis revealed a lack of passivation on the failed parts.
Applications of comparative failure characterisation
Comparative characterisation plays an essential role in industry in diagnosing differences between batches, validating raw materials and preventing repeat failures. Below, we detail its applications in different sectors.
Automotive industry
In the automotive industry, failures in plastic, metal or electronic components can compromise safety. At INFINITIA, we carry out comparative studies to identify causes such as material deviations, manufacturing defects or incorrect treatments.
- Comparison of metal coatings that failed salt spray tests.
- Identification of thermal variations in plastics subjected to temperature cycles.
- Detection of microcracks in metal parts using electron microscopy.
Electronics and energy
The reliability of electronic components depends on their thermal, electrical and structural behaviour. Comparative testing allows defective batches to be detected and quality standards to be improved.
- Study of encapsulants with internal bubbles detected only in failed samples.
- Evaluation of differences in structure and properties.
- Comparison of epoxy resins with different resistance to thermal-operational cycles.
Food industry and packaging
In food packaging and materials, the presence of undesirable migrant substances or differences in functional barriers can compromise safety. Comparative characterisation allows suppliers to be validated and non-conformities to be avoided.
- Identification of undue migration of plasticisers in food films.
- Comparison of sealing properties in defective films versus correct samples.
- Evaluation of thermal resistance of packaging after pasteurisation.
Medical and healthcare sector
In medical devices, even the slightest variation in formulation, biocompatibility or purity can pose a risk. INFINITIA compares materials and manufacturing processes to detect these critical deviations.
- Comparative tests between polymers with different degradation rates.
- Chemical analysis of manufacturing residues in NOK devices.
- Comparison of ageing resistance under disinfection and sterilisation conditions.
Construction
Premature failure of construction materials can lead to high costs. Our comparative studies identify materials that are out of specification or poorly processed.
- Comparison of façade panels with colour loss and cracks.
- Compressive strength analysis of concrete batches with curing defects.
- Abrasion tests on industrial floors with different wear patterns.
Risk reduction and continuous improvement through comparative analysis
In an increasingly demanding industrial environment, comparative fault characterisation has become a strategic tool for companies seeking to control quality, reduce incidents and optimise processes.
At INFINITIA, we offer this service with a rigorous and technical approach, comparing defective samples (NOK) with reference samples (OK) to detect significant differences in their composition, structure or functional properties.
This type of analysis is particularly useful for making quick decisions in supplier validation, raw material control or preliminary studies of recurring failures. Although the failure mechanism is not directly determined, key indicators are obtained that guide future more detailed investigations.
In addition, this service can be complemented by other studies offered by INFINITIA, such as failure mode analysis or more in-depth diagnostics, ensuring a comprehensive view of the problem.
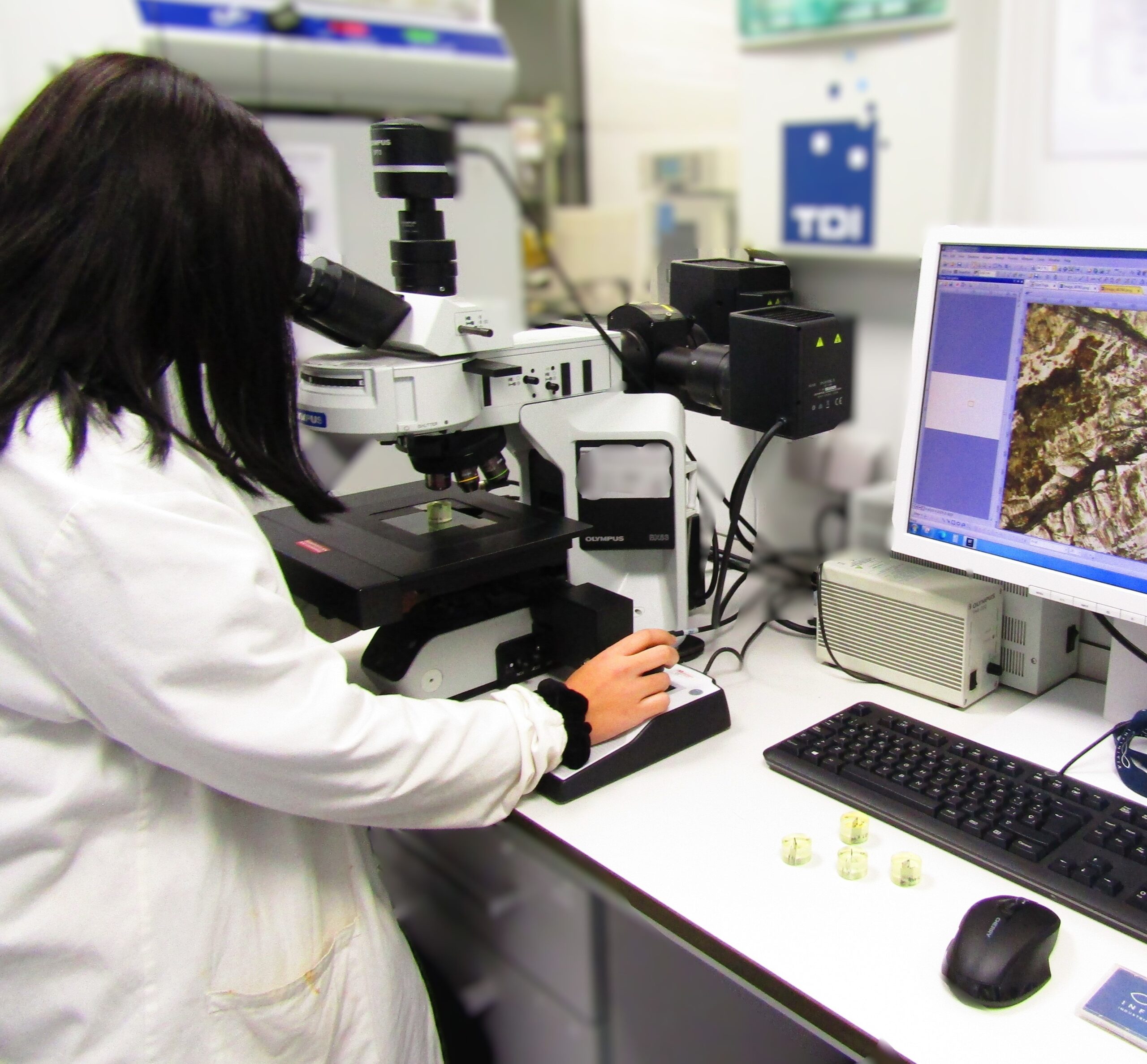
Thanks to our experience in forensic engineering and material characterisation, at INFINITIA we provide our clients not only with accurate data, but also with technical interpretations that are useful for strategic decision-making. Our laboratories are equipped with advanced technology and our professionals work under international quality standards.
In short, relying on INFINITIA to carry out a comparative characterisation of the failure means incorporating a technical ally that adds value at every stage of the analysis process, helping to prevent errors, guarantee quality and increase the competitiveness of products on the market.