Failure mode analysis
At INFINITIA, we carry out failure mode studies to accurately identify the causes of failures in materials, components and industrial systems. This methodology is essential for improving product reliability and processes, especially in sectors where safety and performance are critical.
At INFINITIA, our specialists apply the most advanced technologies in comparative material characterisation, forensic engineering and failure analysis to determine how, when and why a failure has occurred, with the aim of preventing its recurrence.
This service enables companies to anticipate future problems, optimise industrial processes and reinforce the quality of their products.
What is a failure mode study?
Failure mode analysis consists of a detailed technical investigation that analyses defective samples (NOK) by comparing them with others under normal operating conditions (OK).
At INFINITIA, we carry out a comparative characterisation of the materials involved, evaluating parameters such as chemical composition, mechanical properties and service conditions.
We complement this approach with a literature review of similar cases documented in scientific and technical publications, which allows us to contextualise the failure and establish useful correlations for its interpretation. In addition, we request key information from the client, such as the technical data sheet of the component, its service life and operating conditions, which provides a comprehensive view of the problem.
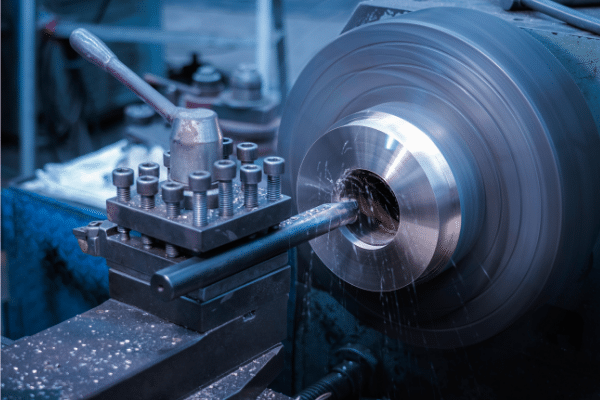
What are the advantages of failure mode analysis?
One of the main advantages of failure mode analysis is the ability to reproduce the failure under controlled conditions. At INFINITIA, we design and perform specific tests that simulate the failure environment to validate the hypotheses put forward.
This approach not only confirms the failure mechanisms identified, but also provides a solid basis for recommending technical solutions and preventing future incidents.
The ability to accurately and quickly diagnose functional failures in industrial components is key to minimising operating costs and avoiding unexpected production downtime.
How is failure mode analysis carried out at INFINITIA?
At INFINITIA, we carry out failure mode analysis as part of a structured process that includes methodologies such as root cause analysis (8D), Failure Mode and Effects Analysis (FMEA) and FMECA (Failure Mode, Effects and Criticality Analysis).
In addition, we use tools such as the Ishikawa diagram and cause-effect probability tables, widely used in quality engineering.
We have a failure analysis laboratory equipped with state-of-the-art technology and a multidisciplinary team with experience in sectors such as automotive, electronics, capital goods and food. Thanks to our rigorous, technical and personalised approach, failure mode studies at INFINITIA are an essential tool for improving the reliability and performance of industrial products.
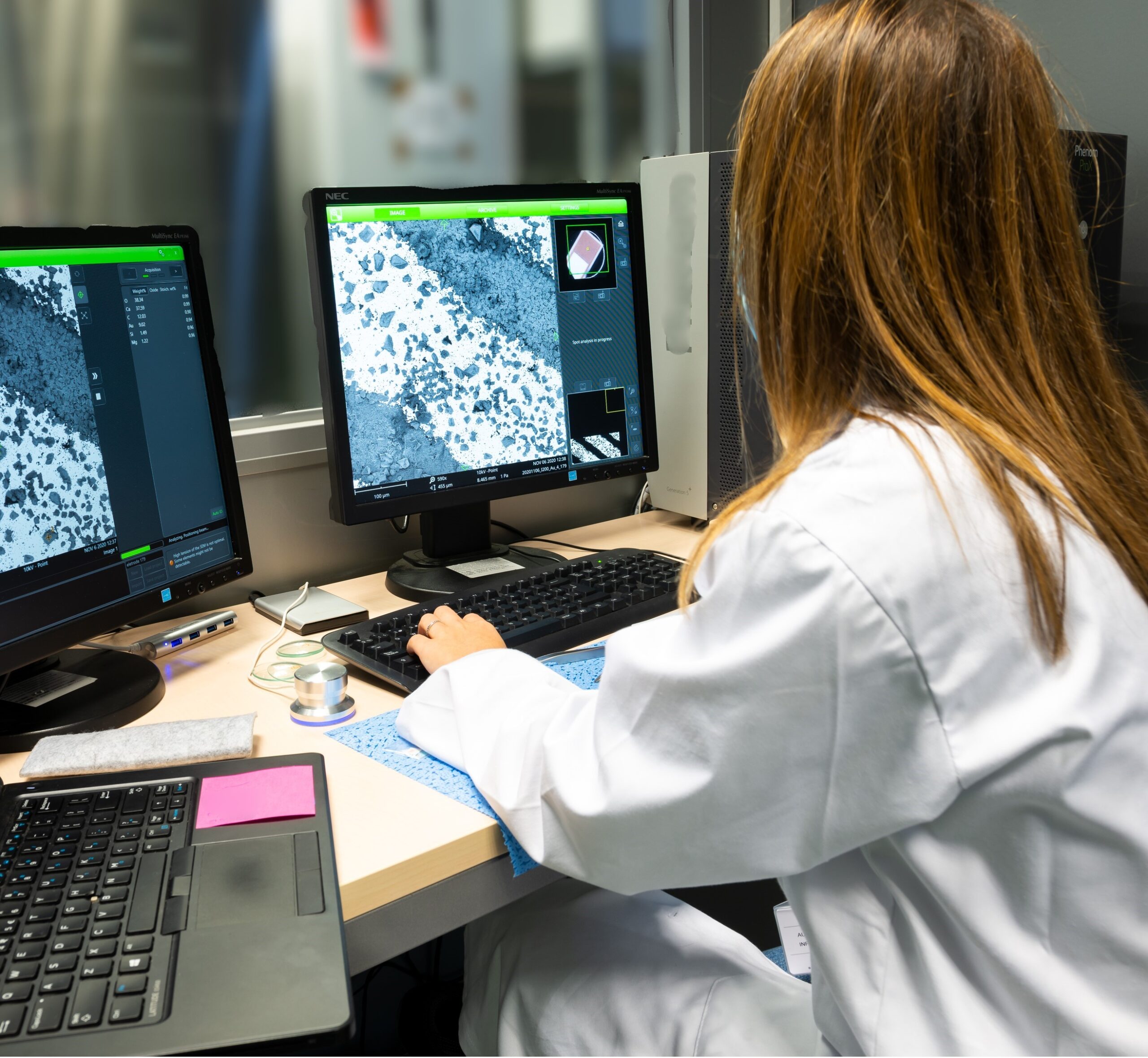
Types of failure mode studies
At INFINITIA, we develop different approaches and techniques to carry out failure mode studies on industrial components. Our goal is to accurately identify failure mechanisms through the technical analysis of defective samples (NOK) compared to correct references (OK), applying advanced diagnostic and validation tools.
Comparative analysis between OK and NOK samples
This type of study allows us to identify differences between faulty and non-faulty parts. At INFINITIA, we use techniques such as spectroscopy, thermal analysis and mechanical testing to detect variations in composition, microstructure or strength that may be related to the functional failure of the component.
For example, in the analysis of a plastic housing for a component, we used infrared spectroscopy to detect a change in the mineral load that was negatively affecting its toughness.
Failure characterisation using microscopy and fractography
Fractography and microscopic analysis allow us to study fractured surfaces and detect clear signs of the failure mechanism, such as fatigue crack propagation, brittle fracture or stress corrosion.
At INFINITIA, we use scanning electron microscopy (SEM) and advanced optics to study critical areas. In a case involving the automotive industry, we identified a crack originating at a stress concentration point on a component that had undergone design improvements.
Reproduction of the failure under controlled conditions
To validate hypotheses, at INFINITIA we design customised tests that simulate the real conditions in which the failure occurred.
This allows us to confirm the root cause and propose robust corrective measures.
For example, in a project involving metal coatings, we reproduced thermal cycles and aggressive atmospheres in a climatic chamber to confirm a failure due to accelerated oxidation.
Documentary studies and technical literature review
At INFINITIA, we carry out a specialised literature analysis that helps to contextualise the failure mode and compare the customer’s case with similar ones. This work allows us to identify proven solutions or common failure trends in certain materials or conditions.
Application of root cause analysis methodologies
We use tools such as the Ishikawa diagram, cause-and-effect flowcharts, the 8D method and Failure Mode and Effects Analysis (FMEA) or its critical variant, FMECA, to structure the diagnosis. These methodologies allow us to prioritise hypotheses according to their criticality and propose specific validation tests.
Applications of Failure Mode Analysis
Failure mode analysis has key applications in multiple industrial sectors. At INFINITIA, we help prevent future incidents, improve product quality and reduce operating costs thanks to a deep understanding of failure in real-world conditions. This tool is especially useful for validating redesigns, selecting alternative materials or correcting production deviations.
Automotive industry
In the automotive sector, components are subjected to mechanical stresses, vibrations, thermal cycles and extreme weather conditions. Early detection of potential failures is essential to ensure the safety, durability and performance of vehicles.
At INFINITIA, we apply advanced techniques to identify failure mechanisms and validate hypotheses through testing under controlled conditions.
- We identify failure mechanisms due to fatigue in metal parts using fractography.
- We reproduce thermal failures in electronic sensors to validate redesigns.
- We apply FMEA to prioritise improvements in critical parts.
Appliances and consumer goods
In this sector, products are designed for prolonged use in a variety of conditions, from humid environments to high temperatures. Functional failures can be caused by variations in raw materials, assembly problems or errors in the material transformation process.
INFINITIA works with manufacturers to analyse and correct these failures, thereby improving the end user experience.
- We detect variations in plastic formulations that affect mechanical strength.
- We use microscopy to reveal poor adhesion between components.
- We carry out comparative studies to validate supplier changes.
Food industry
Food packaging must guarantee product safety and integrity throughout the supply chain. Failure mode studies identify problems such as compound migration, loss of barrier properties or deterioration during heat processing.
At INFINITIA, we help validate materials in accordance with health regulations and optimise their performance on the production line.
- We identify unwanted migrations using chromatography.
- We validate deterioration due to thermal processes in packaging materials.
- We reproduce failures due to freeze-thaw cycles.
Medical and healthcare sector
Medical materials and components are subject to strict standards in terms of biocompatibility, sterilisation and resistance to aggressive media. A failure can compromise patient safety.
That is why at INFINITIA we carry out comprehensive analyses that allow us to validate every part of the design and ensure the functionality of products in real clinical environments.
- We analyse breaks in implantable polymers.
- We study the degradation of materials after sterilisation.
- We apply AMFEC to assess functional risks.
Energy and electronics
Electronic and electrical devices must guarantee reliability in highly demanding thermal and electrical environments. Poor insulation, degradation of encapsulants or ionic migration can cause costly failures.
At INFINITIA, we study power components, sensors and integrated circuits to ensure their performance under thermal, cyclic and environmental loads.
- We detect short circuits caused by metal ion migration.
- We validate epoxy resins under severe thermal cycles.
- We design accelerated ageing tests to simulate years in weeks.
Construction industry
Construction materials are exposed to harsh environments with moisture, UV radiation, temperature changes and chemical agents. In this sector, the correct selection of materials is crucial to prevent structural damage, loss of aesthetic properties or premature deterioration.
INFINITIA analyses failure cases to propose long-lasting technical solutions that comply with regulations.
- We validate the resistance of metal fasteners in saline environments.
- We use cause-effect analysis to identify the failure and propose new materials.
- We evaluate fractures in façade composites by detecting defects in SEM.
Failure mode as a starting point for technical excellence
The study of failure modes is an indispensable tool for any industrial company that wants to ensure the reliability, durability and quality of its products. Understanding the failure mechanism in materials or components not only allows errors to be corrected once they have occurred, but is also key to anticipating them, preventing their recurrence and reducing costs associated with production stoppages or claims.
At INFINITIA Industrial Consulting, we approach each case from a technical and rigorous perspective, combining comparative characterisation of samples, structural analyses, failure simulations under real conditions and bibliographic studies. This enables us to accurately determine the causes of failure and propose corrective or preventive actions with a solid basis.
The application of methodologies such as root cause analysis (8D), Failure Mode and Effects Analysis (FMEA) or AMFEC, together with tools such as the Ishikawa diagram, allows us to prioritise hypotheses, validate solutions and generate useful knowledge for future improvements.
The demand for reliability in sectors such as automotive, electronics, medical and food is constantly growing, and with it the need for advanced and customised analysis.
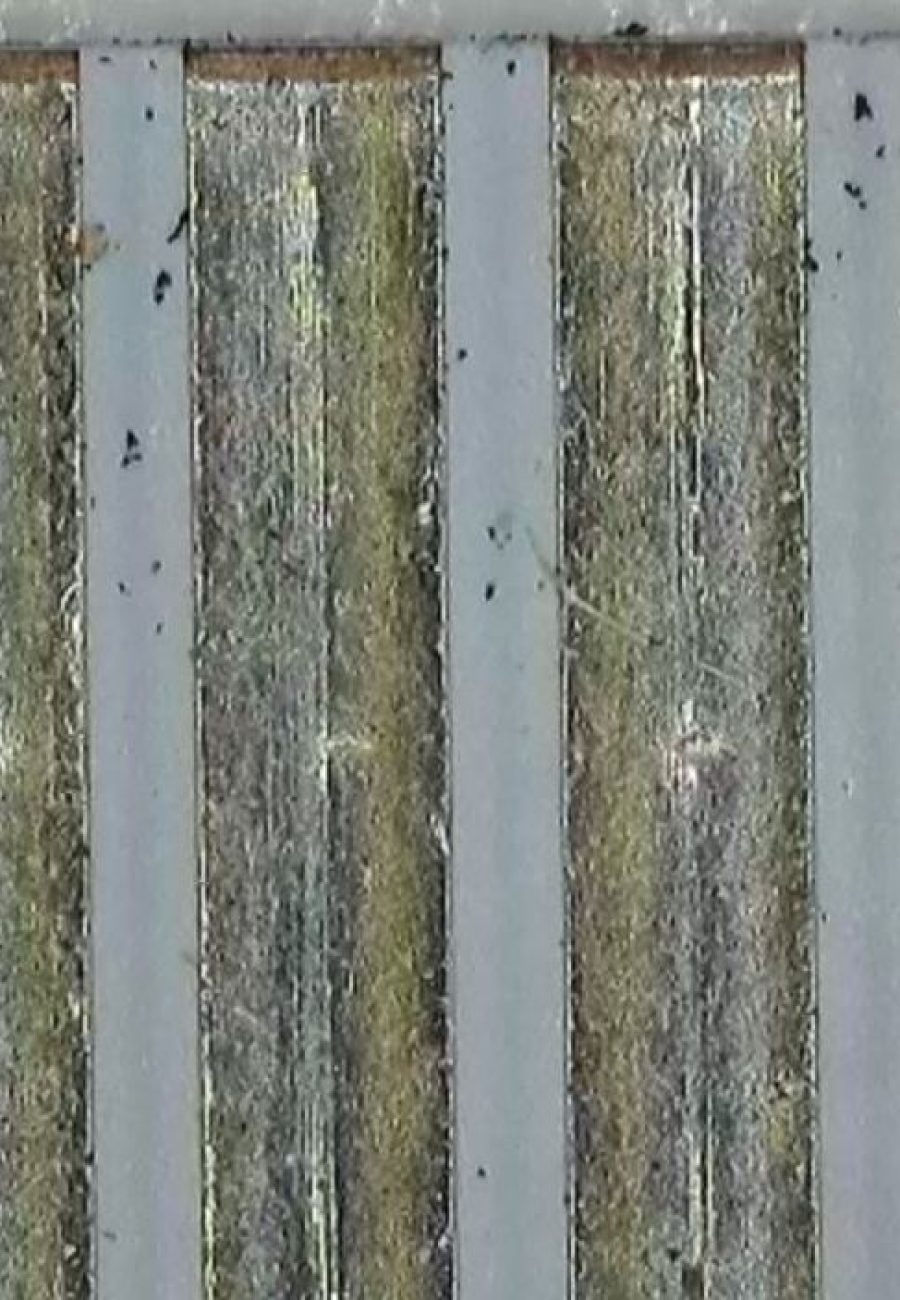
In this context, having INFINITIA as a technology partner allows you to turn a failure into an opportunity for improvement. Our practical, multidisciplinary and results-oriented approach makes each study a strategic investment for companies committed to excellence.