Analysis and improvement of welds
In INFINITIA Industrial Consulting we help you in the welding analysis and in carrying out tests to evaluate and improve the quality of welded joints in various industrial applications. Welding tests are essential to ensure the structural integrity and safety of components used in sectors such as construction, automotive and aerospace.
Our team of forensic engineering specialists and our advanced testing techniques allow us to detect defects through failure analysis, evaluate performance and optimize welding processes. We assure you a high level of quality and reliability!
What is welding analysis?
The welding analysis it consists of a series of tests and evaluations that are carried out to verify the quality of the welded joints and ensure that they meet the required safety and performance standards. This analysis includes bothdestructive welding testing as non-destructive welding testing. Each of them with the purpose of identifying defects, evaluating the strength and durability of the joints, and optimizing the welding procedures.
These tests can detect problems such as porosity, cracks, inclusions or lack of penetration, which can compromise the structural integrity of the welded component. They are therefore essential for the manufacture of bridges, high-pressure pipes or aeronautical structures, among others.
Contact with us
Contact us for more information or, if you prefer, you can use one of our other technical consultancies with complementary services to boost your project.
Types of welding tests
Welding tests are methods used to evaluate the integrity and quality of welded joints, ensuring that they comply with the technical and regulatory specifications of the project.
Discover the different types of tests that are used depending on the objectives of the analysis and the characteristics of the welded material:
- Welding bending test: This is a destructive method used to assess the ductility and strength of a weld. A controlled bending force is applied to a welded sample until significant deformation or even rupture is achieved. It allows the identification of internal defects, such as lack of fusion or inclusion of impurities, which can compromise the ability of the welded joint to with stand loads without fracturing. It is very useful in construction, where welded joints must with stand extreme deformations and loads.
- Ultrasonic testing in welding: This non-destructive method uses ultrasonic waves to assess the internal integrity of welds. Sound waves are sent through the welded material and reflected off the boundaries of internal discontinuities such as cracks or pores. By analysing the timing and amplitude of the received echoes, internal defects can be identified and sized without damaging the part. It is ideal for applications where internal inspection is crucial, such as in high-pressure welds and aerospace structures.
- Welding Penetrant Testing: non-destructive method used to detect surface discontinuities such as cracks, pores or weld defects that are not visible to the naked eye. A high-capillarity liquid is poured onto the surface of the material, penetrating the cracks and defects. The excess liquid is then removed and a developer is applied to highlight the defects, making them easier to detect visually. This allows the surface integrity of welds in critical components such as pipelines and pressure vessels to be verified.
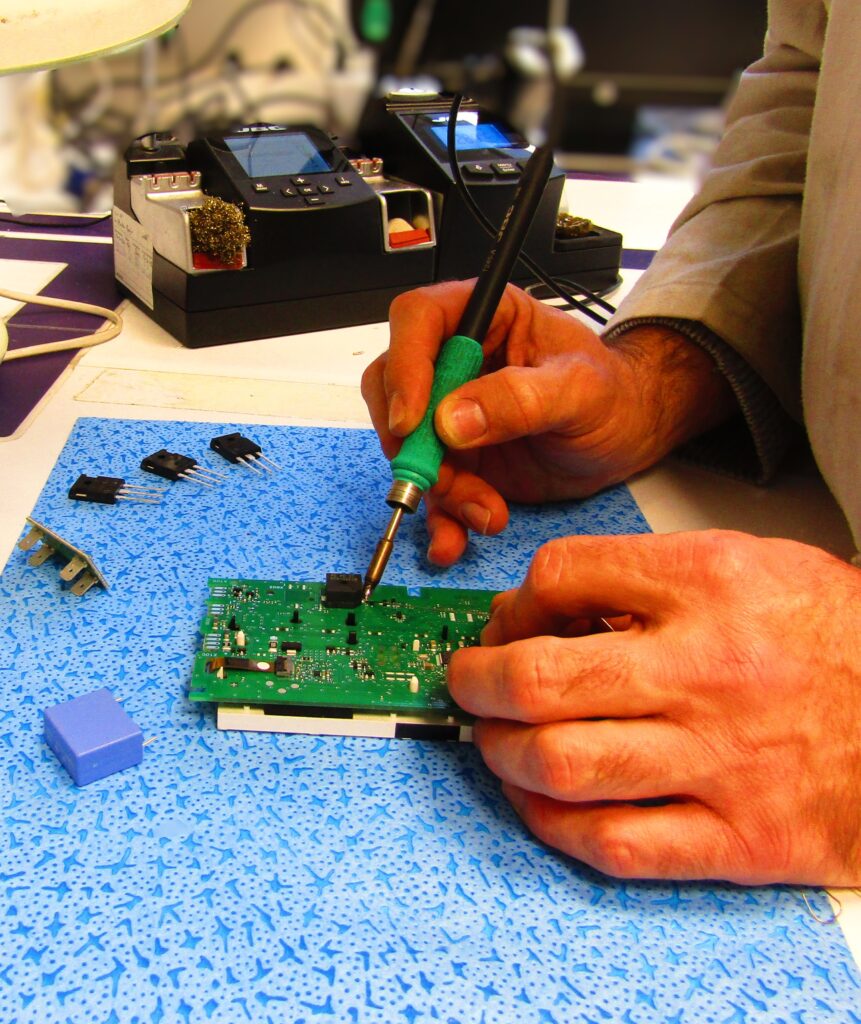
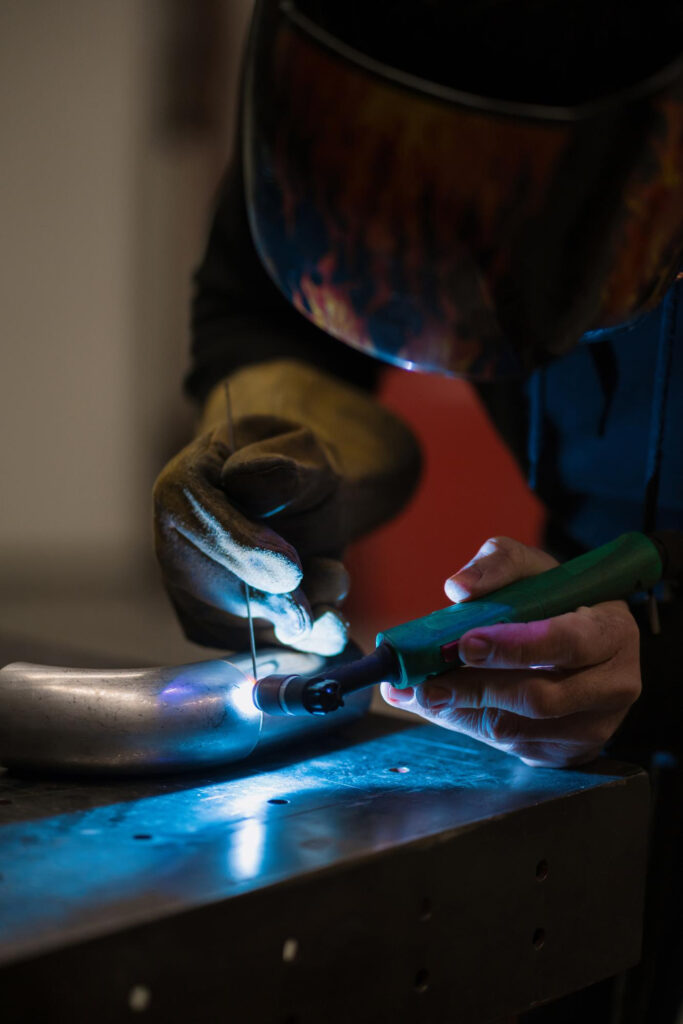
What are destructive welding tests?
The destructive welding testing consist of the controlled destruction of the piece to evaluate its mechanical and structural properties. They provide precise data on the strength, ductility and toughness of the welded joints.
Below are the most commonly used types of destructive testing:
- Tensile test: An axial force is applied until the sample breaks to measure the strength and elongation of the weld. It allows the quality of the weld to be evaluated in comparison with the base material.
- Impact test: Evaluates the toughness of the weld under impact conditions. It is essential to determine how the weld will behave under dynamic conditions of use or in cold environments, where materials tend to become more brittle.
- Macrography test: This involves cutting and polishing a section of the weld to observe its internal structure. It helps us identify defects such as porosity, slag inclusions or lack of fusion.
These tests on metallic materials and alloys are essential to ensure that welds meet strength and safety requirements in critical applications where failure could have serious consequences. For example, in the construction of bridges or on oil platforms.
Types of non-destructive welding testing
The non-destructive welding testing evaluate the quality and integrity of welds without damaging the component. These methods are ideal for the welding inspection in critical structures where the integrity of the part cannot be compromised.
We find different types of non-destructive testing:
- X-ray test: Uses X-rays or gamma rays to create images of the weld, allowing detection of internal defects such as porosity, cracks and lack of fusion. It is especially useful for analysis of welds in high pressure pipes and components, where these defects can compromise safety.
- Magnetic particle testing: A magnetic field is applied to the weld and magnetic powder is used to detect surface and subsurface defects. Defects in the material disrupt the magnetic flux and the powder accumulates in these areas, making the defects visible. Very effective for inspecting welds in ferromagnetic materials such as steel and iron.
- Ultrasound test: It uses ultrasonic waves to detect internal discontinuities without damaging the material. It is key to inspecting welds in thick materials and detecting defects in the weld volume, which are not visible externally.
These tests allow a detailed and precise evaluation of the weld, ensuring quality and safety without affecting the functionality of the inspected component.
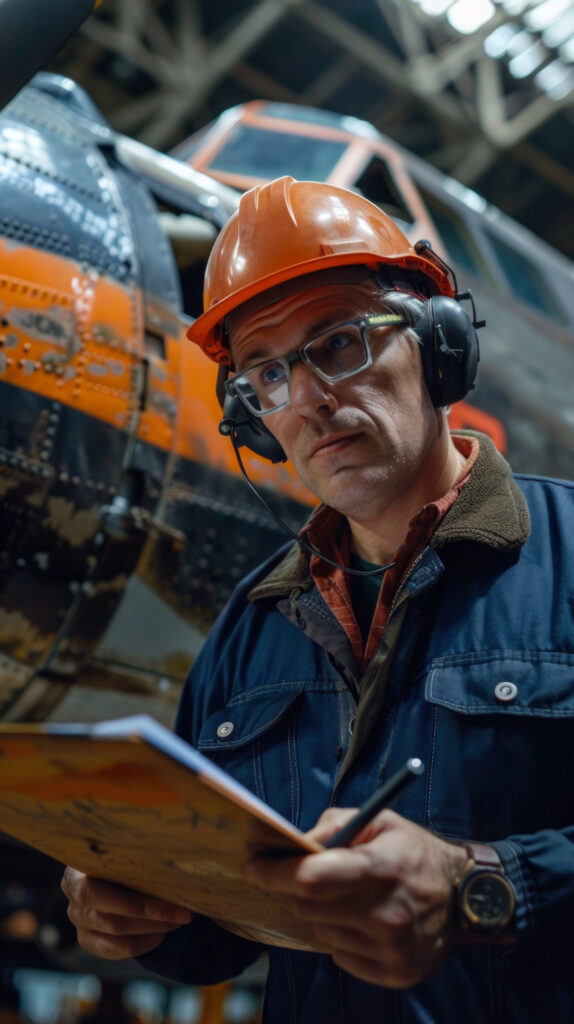
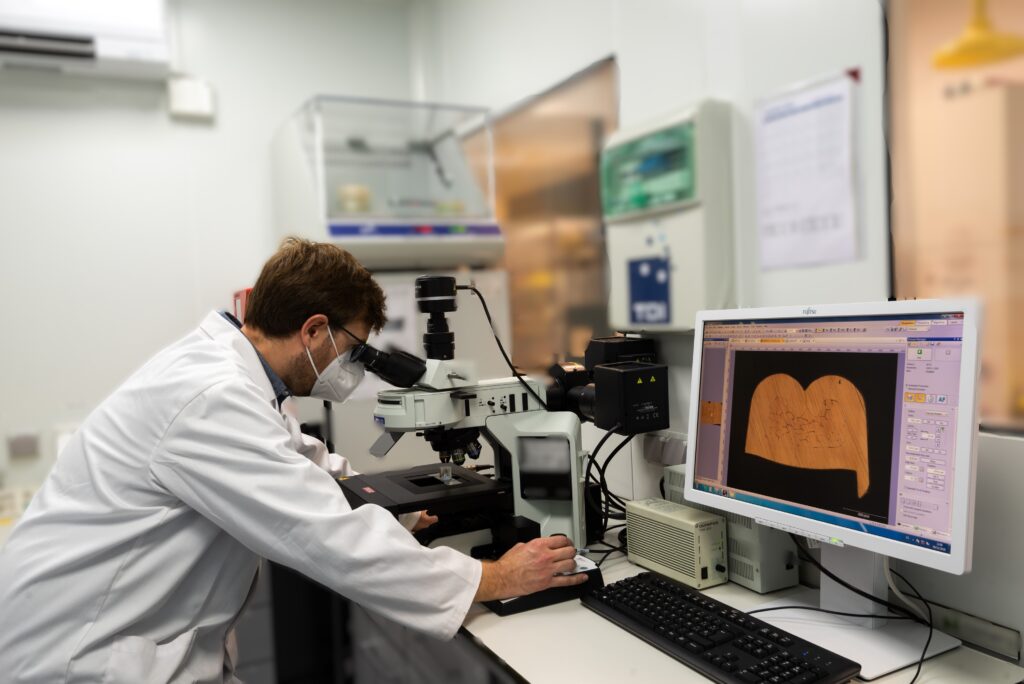
What are welding tests on structures?
The welding tests on structures are critical to ensuring the safety and durability of structures subjected to extreme loads and conditions. From bridges and buildings to industrial infrastructures such as power plants and offshore platforms.
The objective is to ensure that welds can withstand the stresses and deformations to which they will be exposed during their service life. Both destructive and non-destructive tests are used to verify that welded joints do not present defects that could compromise structural integrity.
Periodic assessment through non-destructive testing is also key to the inspection and preventive maintenance of existing structures, avoiding catastrophic failures and ensuring long-term safety.
Benefits of welding analysis and improvement in INFINITIA
Trust us for the welding analysis, discover all its advantages:
- Accurate and complete evaluations: We use the most advanced techniques to carry out exhaustive tests that allow us to detect any defects, evaluate resistance and optimize welding procedures. In this way, each welded component will meet the highest quality and safety standards.
- Welding process optimization: Based on the results of our tests, we offer recommendations for improving welding processes, including the selection of appropriate welding parameters and the optimization of preparation and post-welding techniques. This not only improves the quality of welded joints, but also reduces time and costs.
- Compliance with regulations and standards: We support our clients to ensure that the welds analyzed comply with international regulations and standards, such as AWS, ISO and ASME, ensuring that products and structures meet the most demanding safety and performance requirements.
Prevention of structural failures: We identify and correct defects in welds before they become critical problems. We prevent structural failures that can have serious consequences, especially in applications where safety is paramount, such as bridges and support structures.
INFINITIA: We are experts in welding tests in the development and maintenance of structures
In INFINITY we collaborate with our clients from the earliest stages of development and design of structures to ensure that the welds meet the requirements of strength and durability.
From our laboratory, we carry out specific tests to validate the quality of welded joints and propose improvements in welding procedures to optimize their performance. In addition, we offer services of inspection and maintenance for existing structuresusing non-destructive testing that allows the condition of the welds to be assessed without the need for costly repairs or affecting operations. A complete guarantee of safety and long-term structural integrity, minimising the risk of unexpected failures.
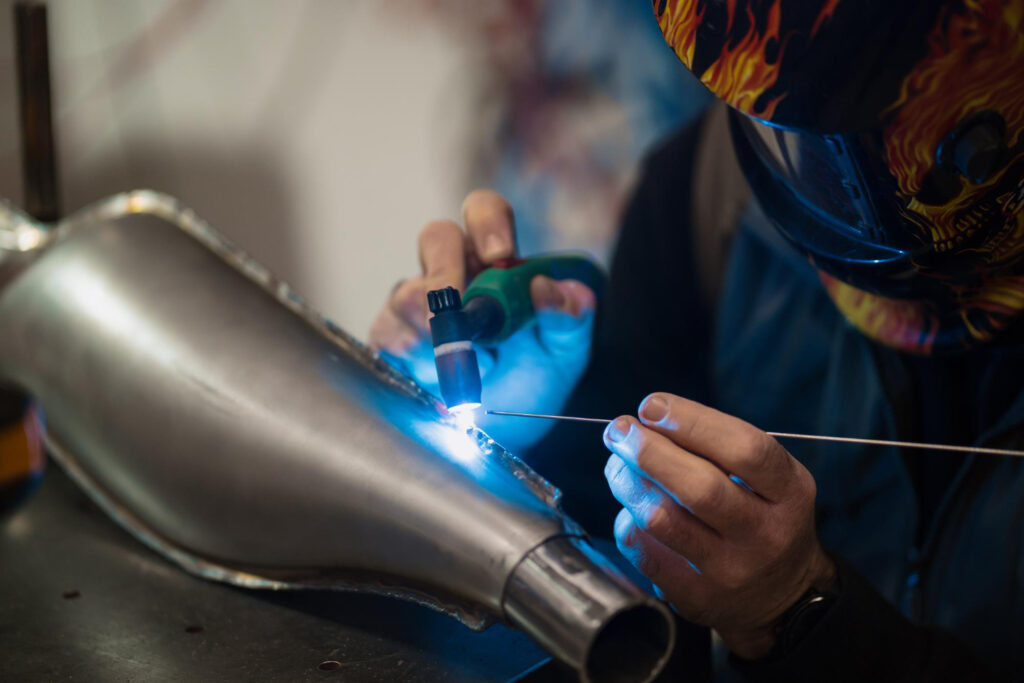
Contact INFINITIA for welding analysis and improvement
If you are looking for services in welding analysis and optimization of welding processes, at INFINITIA Industrial Consulting we can help you. Our team of specialists and our advanced equipment allow us to offer precise and reliable results for any type of industrial application.
Contact us for more information or, if you prefer, you have other of our options available technical consultancies with complementary services to enhance your project.
Contact with us
Contact us for more information or, if you prefer, you can use one of our other technical consultancies with complementary services to boost your project.