What was the challenge or problem to solve?
An important client, a manufacturer of industrial electronics, presented us with this challenge when, during one of the stages of the production process, they detected aesthetic defects in certain electronic components.
The particularity of this case was that no apparent modification had been made to the production process that could be identified as the cause of this change.
The main objective of the INFINITIAās Forensic Engineering team was to determine which compound used during its manufacture was responsible for this aesthetic defect. This challenge involved not only identifying the underlying cause of the problem but also selecting the appropriate analytical techniques to conduct the investigation efficiently and effectively.
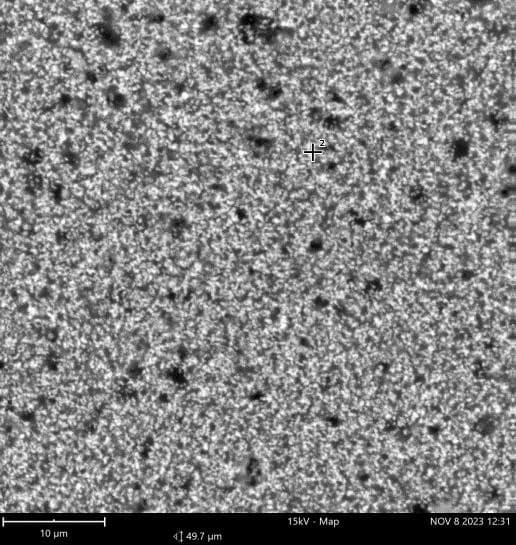
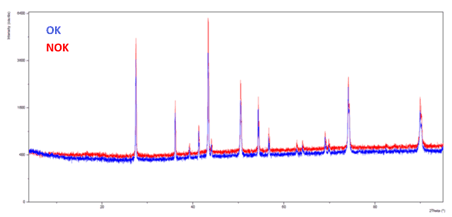
To tackle this challenge, the Forensic Engineering team began by preparing the compound samples to ensure their suitability for the laboratory equipment needed to perform the proposed analyses.
Next, a detailed visual inspection was carried out using scanning electron microscopy (SEM), a key technique for examining the morphology and structure of the samples at the microscopic level.
Finally, the analysis of the compound’s composition was deepened using techniques such as the X-ray detector (EDX) coupled to an SEM microscope, and X-ray diffraction spectroscopy (XRD). EDX provided a semi-quantitative view of the sample’s composition, while XRD offered a more detailed qualitative and quantitative analysis of the composition. This combination of techniques allowed the team to rule out the presence of impurities or structural changes that could be responsible for the aesthetic defect.
Based on these results, a report was prepared in which the root-cause diagnosis was proposed, allowing the client to narrow down the problem and take corrective measures in the factory to solve it.