What was the challenge or problem to solve?
The need of one of our clients to manufacture spare parts without digital or documentary backups presented a significant challenge, especially when it came to parts with high geometric complexity. This situation was further complicated by the dependence on a single supplier for the manufacturing of spare parts, which significantly restricted negotiation and adaptation options in the face of price variations or disruptions in the production of such parts.
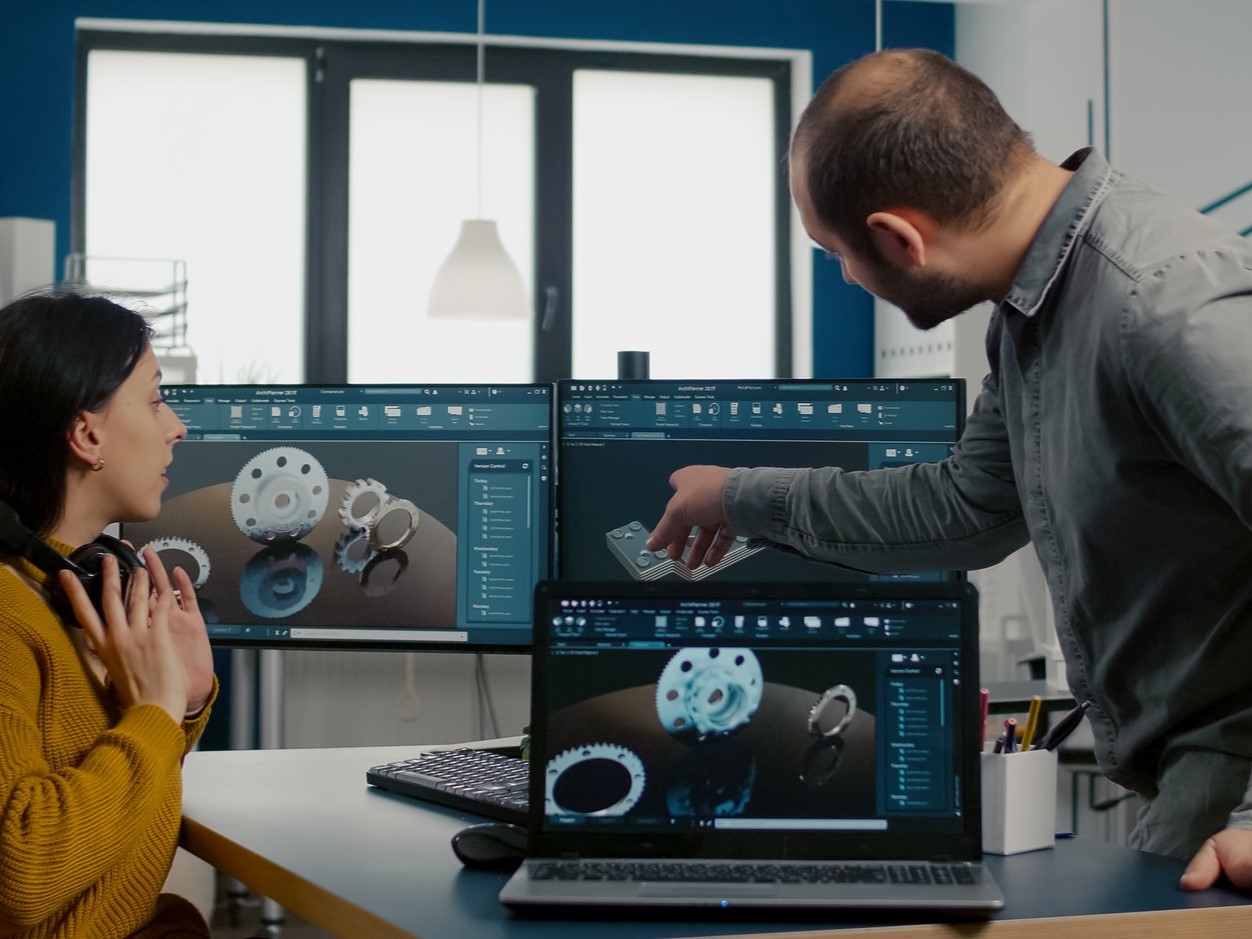
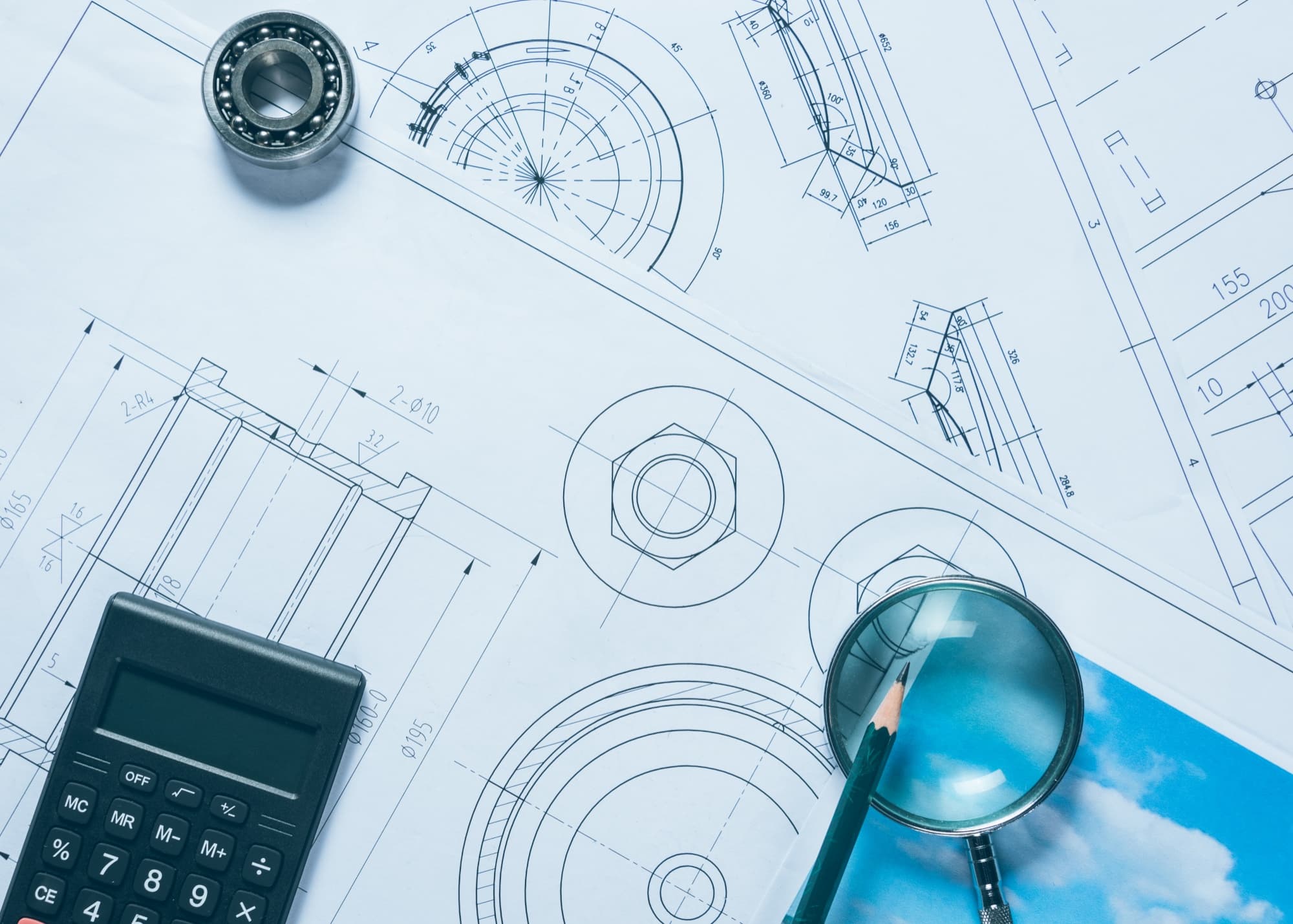
The process began with the preparation of the physical parts for their 3D scanning, using a high-precision scanner capable of capturing details with a maximum deviation of ±25μm. This technology allowed for obtaining a detailed point cloud of the geometry of the parts, a crucial step for accurately replicating the parts.
Using professional CAD software, this point cloud was transformed into parametric 3D models in the standardized STP format, faithfully replicating the original parts. This model served as the basis for the development of detailed CAD drawings, specifying dimensions and tolerances essential for manufacturing.
The implemented solution not only allowed for the generation of 100% functional spare parts but also provided our client with technical documentation and a list of potential suppliers, facilitating the manufacture of the necessary parts without depending on a single supplier. This approach ensured greater autonomy in spare parts production, representing a notable success for the Product Development team, demonstrating the effectiveness of reverse engineering in overcoming manufacturing challenges.