¿Cuál fue el reto o problema a resolver?
La fabricación de moldes de inyección representa un pilar fundamental en la industria del plástico, permitiendo la producción en masa de componentes con precisión y eficiencia. Sin embargo, enfrenta desafíos significativos, especialmente en términos de costos y tiempos de producción.
En este contexto, un cliente planteó la necesidad de explorar alternativas a los métodos convencionales de fabricación de moldes, que pudieran reducir tanto el costo como el tiempo requerido, sin comprometer su rendimiento. El proyecto en cuestión tuvo como objetivo validar la tecnología de impresión 3D DLP para la fabricación de insertos de moldes de inyección de bajo coste.
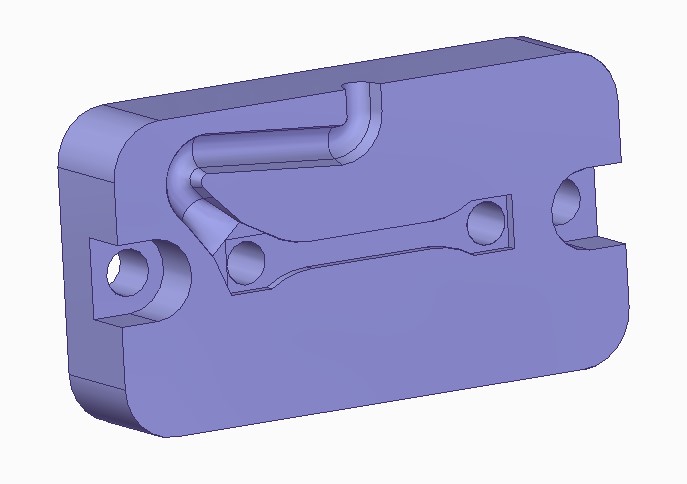
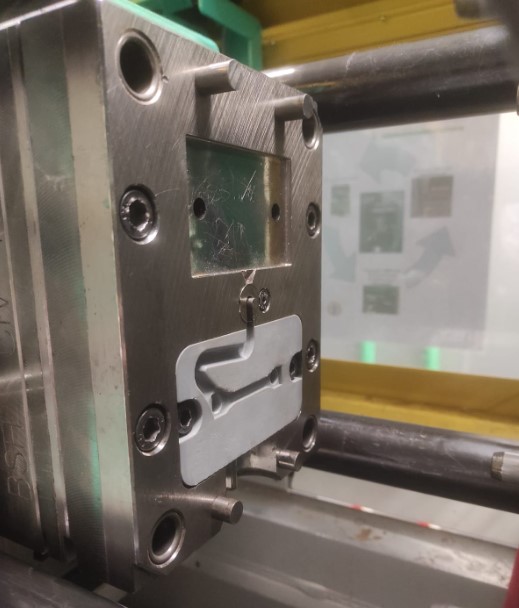
Posteriormente, se procedió a la impresión 3D del molde utilizando una resina especial de alta temperatura. La dificultad del proyecto radicaba en que el molde debía de soportar sin deformarse las condiciones extremas durante el proceso de inyección, lo cual era crucial para garantizar la durabilidad y la eficacia del molde. La tecnología DLP, conocida por su precisión y calidad en la fabricación de piezas, se utilizó para producir el molde con un detalle y una fiabilidad excepcionales.
Con el molde ya fabricado, se llevaron a cabo pruebas de inyección con probetas estandarizadas, utilizando tanto el molde impreso en 3D como un molde convencional para comparar los resultados. La caracterización mecánica y el análisis superficial de las probetas revelaron que las piezas obtenidas con ambos tipos de moldes presentaban propiedades muy similares, tanto en términos de resistencia mecánica como de acabados superficiales. Estos hallazgos demostraron que los moldes fabricados mediante impresión 3D DLP no solo son viables para la producción de piezas por inyección, sino que también ofrecen una alternativa de bajo coste y rápida fabricación, sin comprometer la calidad de las piezas producidas.