¿Cuál fue el reto o problema a resolver?
El cliente quiso rediseñar unas piezas con requerimientos de estanqueidad interna que estaban presentando fugas durante las pruebas de laboratorio.
El cliente contaba con un diseño con el que consideraba que se debía mantener la estanqueidad del conjunto pero siempre presentaba pérdidas durante las pruebas por lo que no tenía claro a qué se debían estas.
El cliente nos facilitó unos modelos CAD básicos que había preparado usando las herramientas y conocimientos a su disposición pero no contaba con una experiencia muy extensa en el diseño de este tipo de piezas.

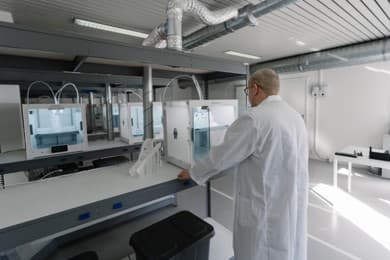
¿Cómo se abordó o cuál fue la solución?
En primer lugar, el equipo de prototipado analizó los modelos 3D que nos facilitó el cliente con un programa CAD profesional para analizar la causa de los posibles fallos de estanqueidad del conjunto y se detectaron una serie de interferencias y fallos de alineación entre las piezas que eran las causantes directas de dichas fugas.
A continuación se planteó un rediseño optimizado de las piezas originales que facilitarían tanto el montaje como el testeo de dichas nuevas piezas y se produjeron prototipos mediante impresión 3D en resina transparente, la cual permitió visualizar el comportamiento de los fluidos dentro de las piezas.
Finalmente se pudo iterar hasta conseguir un diseño óptimo, funcional y 100% libre de fugas con el que el cliente quedó satisfecho.
El reto
- Analizar la causa del fallo de estanqueidad de las piezas
- Plantear un rediseño que solucionara los problemas actuales
- Verificar la validez del nuevo diseño
La solución
- Uso de programas CAD profesionales para analizar el diseño de las piezas del cliente
- Rediseño del sistema de estanqueidad entre ambas piezas
- Verificación mediante impresión 3D en resina transparente la total estanqueidad del nuevo diseño