¿Cuál fue el reto o problema a resolver?
El equipo de Ingeniería Forense de INFINITIA se enfrentó al reto de realizar una ingeniería inversa de residuos metálicos. El cliente encontró unas partículas en unos filtros de aire en un determinado proceso de producción. El objetivo era conocer la composición elemental de las partículas para entender su origen, su impacto en el proceso productivo y cómo esto podía estar afectando a la calidad del producto final.

La calidad del aire en ciertos procesos productivos es crítica (por ejemplo, en procesos de pintado o pegados), y es por ello que se utilizan filtros de partículas para conseguir acabados de mayor calidad. Sin embargo, en ciertas ocasiones un mal mantenimiento de los filtros, o bien una incidencia externa a la fábrica, puede minimizar la eficiencia del filtrado y por tanto disminuir la calidad de las piezas fabricadas, pudiendo aparecer defectos de pintado, aparición de burbujas, o problemas con el proceso de pegado.
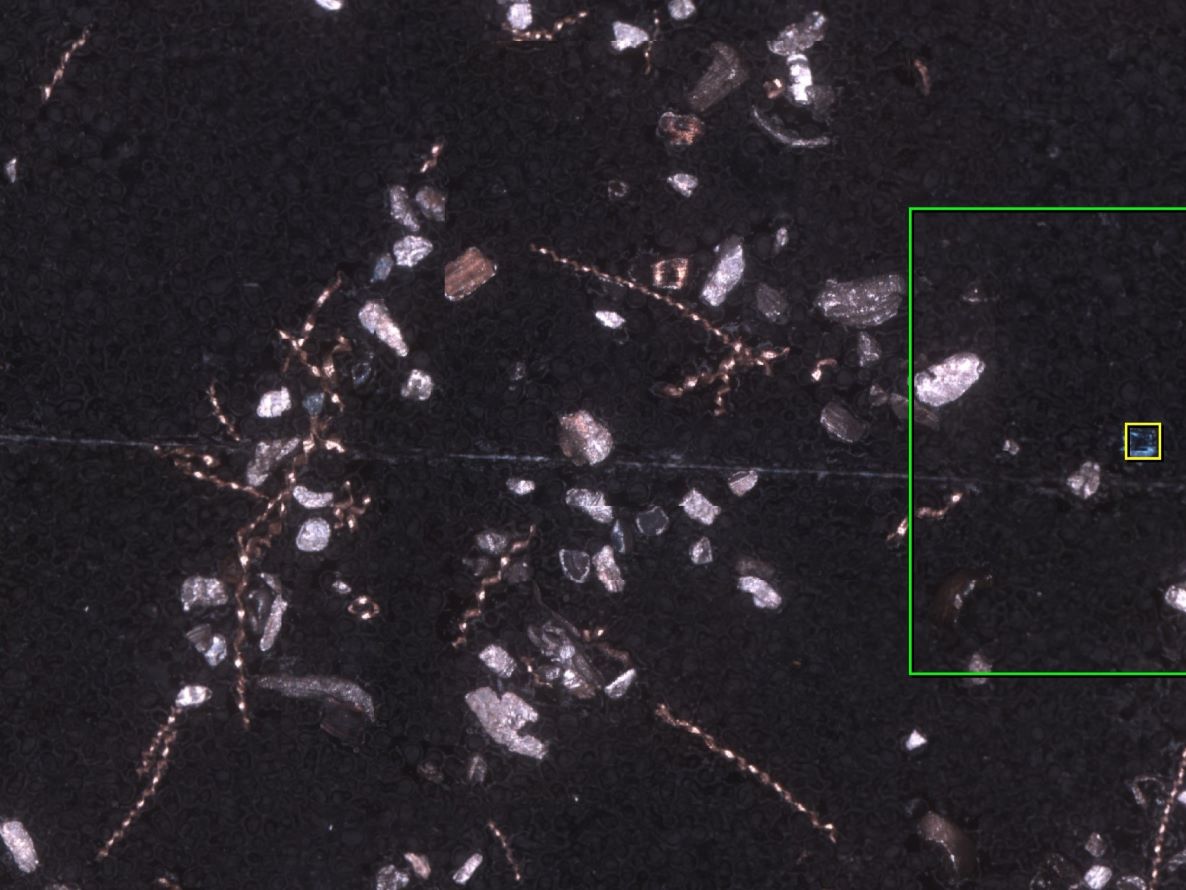
Para enfrentar este desafío, el proyecto se estructuró en varios pasos. Inicialmente, se recibió el material particulado de los filtros y se realizó un examen visual con ayuda de un microscopio óptico. Esta primera inspección visual sirvió para obtener una comprensión preliminar de las características generales de las partículas, lo cual guio las etapas subsiguientes de análisis más detallados. El paso crucial fue el empleo de la microscopía electrónica de barrido, combinada con espectroscopía de rayos X de energía dispersiva (SEM-EDX).
Esta tecnología avanzada permitió no solo visualizar la morfología de las partículas con alta resolución, sino también identificar de manera precisa su composición elemental. Este análisis fue fundamental para diferenciar las partículas según su tipo y determinar la homogeneidad en su composición en diferentes puntos de cada partícula.
Finalmente, se capturaron imágenes detalladas y se realizaron mediciones de la composición elemental, empleando herramientas de software especializadas. Estos datos permitieron una evaluación exhaustiva de la variabilidad de las partículas y facilitaron la interpretación de los impactos potenciales en el proceso productivo. Los resultados fueron compilados y presentados de manera clara y comprensible, proporcionando al cliente una base sólida para implementar mejoras significativas en sus protocolos de fabricación.
Este enfoque detallado no solo resolvió el problema inicial, sino que también fortaleció la capacidad de nuestro cliente para controlar y optimizar sus procesos de producción, asegurando así una mayor calidad y minimizando los defectos en el producto final.