¿Cuál fue el reto o problema a resolver?
El proyecto surgió a raíz de un desafío planteado por un cliente que había desarrollado un dispositivo con la ayuda de otra empresa. El cliente necesitaba mantener el diseño general del dispositivo, pero era imperativo reducir el número de piezas para reducir costes de producción y de ensamblaje.
Tras la valoración de INFINITIA del diseño que planteaba el cliente, se determinó como el diseño inicial del dispositivo era complejo, contando con un número excesivo de piezas y elementos de anclaje, lo que resultaba en un proceso de ensamblaje costoso y laborioso.
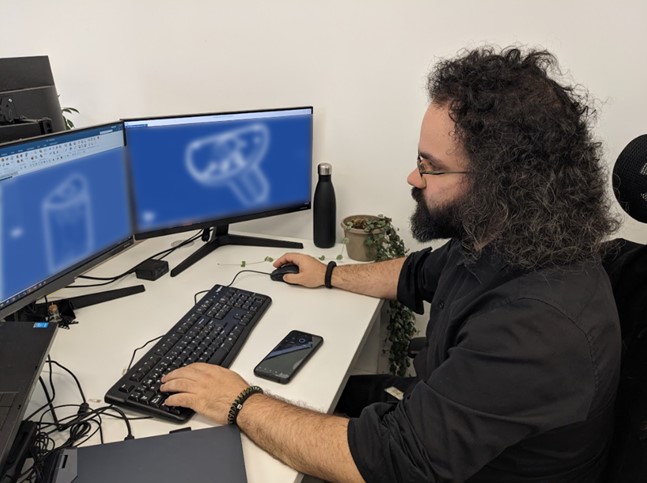
El reto se consideró superado con éxito cuando se logró reducir el dispositivo a solo cuatro piezas, utilizando únicamente ocho tornillos idénticos. Este avance no solo disminuyó los costos de fabricación y ensamblaje, sino que también simplificó significativamente el proceso de montaje. El equipo de Desarrollo de Producto de INFINITIA demostró su competencia y creatividad al abordar este complejo desafío, entregando un producto optimizado y eficiente.
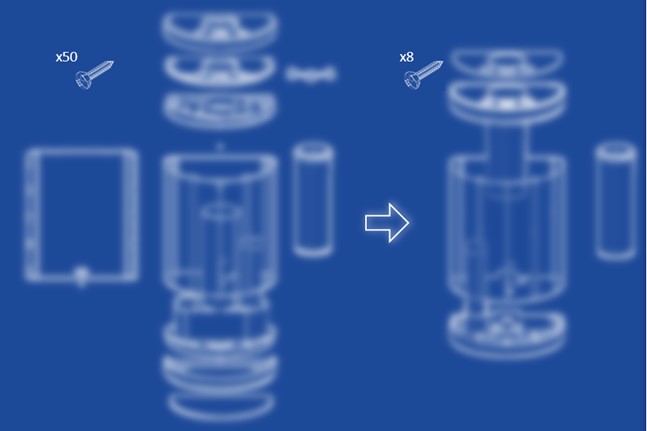
El primer paso en el proyecto fue un análisis detallado del diseño original del dispositivo y de las necesidades específicas del cliente. Se utilizó software CAD profesional para examinar el diseño, identificando las funcionalidades esenciales y agrupando las geometrías necesarias para cumplir con los requisitos del cliente. Este análisis permitió comprender a fondo el dispositivo y determinar qué componentes eran realmente indispensables.
Con una clara comprensión de las funcionalidades y geometrías, se procedió al rediseño del dispositivo. Aprovechando el know-how del equipo de Desarrollo de Producto en diseño de piezas y mecanismos de anclaje, se unificaron elementos y se eliminaron componentes superfluos. El uso de técnicas avanzadas de diseño permitió crear modelos más eficientes que requerían menos piezas y tornillería, favoreciendo un enfoque innovador frente a métodos más tradicionales.
Posteriormente, las nuevas geometrías fueron fabricadas mediante procesos de prototipado rápido utilizando fabricación aditiva de alta calidad. Las impresoras 3D de diversas tecnologías permitieron iterar los diseños hasta alcanzar la solución óptima sin incurrir en altos costos ni largos plazos. Este método facilitó la validación y ajuste del diseño antes de la fase de industrialización.
Finalmente, se realizó el montaje y testeo de los prototipos demostradores. Utilizando equipos de postprocesado y acabado estético profesional, se crearon modelos que permitieron al cliente presentar el producto a accionistas e inversores como si se tratara del dispositivo final. Esta etapa fue crucial para asegurar la aceptación y éxito del rediseño.
En resumen, el enfoque integral y meticuloso adoptado por INFINITIA resultó en una solución exitosa que no solo cumplió con los objetivos del cliente, sino que también optimizó significativamente el diseño y producción del dispositivo.